Summary:In the intricate dance of industrial machinery, the often-overlooked heroes ensuring seamless operations are the rubber flat belts. These unassuming components play a critical role in conveying materials, powering machinery, and facilitating processe......
In the intricate dance of industrial machinery, the often-overlooked heroes ensuring seamless operations are the rubber flat belts. These unassuming components play a critical role in conveying materials, powering machinery, and facilitating processes across diverse industrial sectors. However, their effectiveness is contingent upon meticulous maintenance and regular inspections to prevent unexpected failures that can disrupt productivity and incur costly downtime.
Regular Inspection: Regular visual inspections serve as the primary line of defense against unexpected failures. It involves a meticulous examination of the entire length of the rubber flat belts, checking for any signs of wear, tear, or damage. This proactive approach allows maintenance personnel to identify potential issues in their early stages, preventing minor concerns from escalating into major problems.
Tension Monitoring: Tension monitoring is not a one-size-fits-all task. It involves precision and attention to detail. Utilizing tension measurement tools, maintenance teams can ensure that the rubber flat belts are operating within the specified tension range. Regular adjustments are made to counteract factors such as belt stretching, ensuring optimal tension and preventing complications like slippage and premature wear.
Alignment Checks: Misalignment of pulleys is a silent adversary that can wreak havoc on rubber flat belts. Advanced laser alignment tools are employed to meticulously assess the alignment of pulleys, ensuring they are perfectly synchronized. This meticulous approach not only extends the life of the belts but also enhances the efficiency of the entire industrial system.
Environmental Factors: Delving into the environmental considerations, this involves a thorough analysis of the operating conditions. From extreme temperatures to exposure to corrosive chemicals, each factor is carefully evaluated. In response, engineers may recommend specific rubber formulations or coatings to fortify the belts against environmental stressors, ensuring longevity and optimal performance.
Cleanliness: Cleanliness is not merely a superficial concern. It's a proactive strategy to combat premature wear. Industrial settings are rife with dust, debris, and contaminants that, if left unchecked, can embed themselves in the rubber surface, accelerating wear. Regular cleaning protocols, perhaps employing specialized cleaning agents, become an integral part of the maintenance routine.
Lubrication: Lubrication is elevated to a science in the maintenance regimen. The right lubricants, applied at precise intervals, ensure that the pulleys and bearings operate with minimal friction. This not only extends the life of the rubber flat belts but also contributes to the overall efficiency of the machinery by reducing energy losses due to friction.
Belt Speed Monitoring: Belt speed monitoring involves more than just checking a numerical value. It requires sophisticated monitoring systems that track real-time speeds and ensure they align with the specified parameters. Any deviations trigger immediate attention, preventing not only excessive wear on the belts but also safeguarding against potential catastrophic failures.
Inspection of Belt Edges: Inspecting the edges of rubber flat belts is akin to reading the story of their interaction with pulleys and other components. Fraying or irregularities at the edges can unveil misalignment issues or even hint at problems within the pulley system. This detailed inspection becomes a diagnostic tool, guiding maintenance teams to address root causes.
Monitoring for Excessive Vibrations: Excessive vibrations are not merely nuisances; they are early warning signals. Advanced vibration monitoring systems are employed to detect abnormal oscillations. Addressing the source of these vibrations becomes a proactive strategy to prevent wear and tear on the rubber flat belts, preserving their integrity and functionality.
Industrial Rubber Flat Belt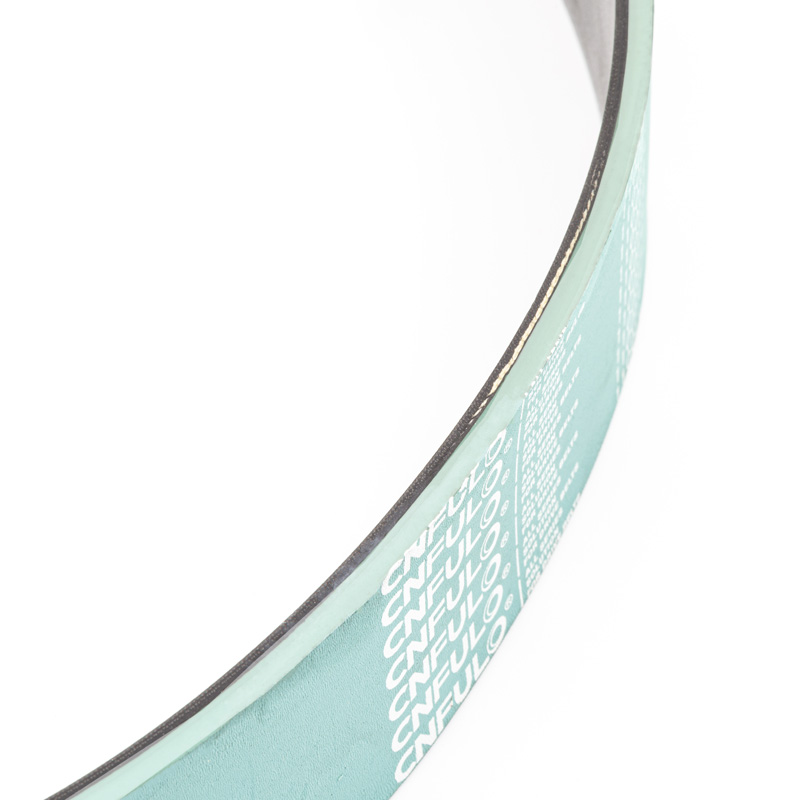