Summary:The industrial transmission belts play a pivotal role in power transmission, conveying motion and energy efficiently across diverse applications. To ensure the seamless operation of these belts and extend their service life, a proactive approach to m......
The industrial transmission belts play a pivotal role in power transmission, conveying motion and energy efficiently across diverse applications. To ensure the seamless operation of these belts and extend their service life, a proactive approach to maintenance is paramount.
Regular Inspection: Conduct meticulous visual inspections at regular intervals. Examine the entire length of the industrial transmission belt, scrutinizing for any signs of wear, abrasion, or irregularities. Use magnification tools for detailed assessments, focusing on potential stress points around pulleys, edges, and joints. Implement a comprehensive checklist that includes aspects such as belt tension, alignment, and surface condition. Early detection through a thorough inspection routine allows for proactive maintenance, minimizing the risk of unexpected failures.
Proper Tensioning: Precision in tensioning is not just a guideline; it's a science. Utilize advanced tension measurement tools, such as sonic or laser alignment devices, to ensure the industrial transmission belt is precisely tensioned according to manufacturer specifications. Develop a nuanced understanding of tension variations under different loads and operating conditions. Striking the delicate balance between optimal tension and avoiding over-tensioning or under-tensioning is crucial for maximizing the belt's operational life and minimizing the strain on associated components.
Alignment Checks: Aligning pulleys and sheaves is not a one-time task but an ongoing process. Employ cutting-edge laser alignment technologies to achieve and maintain precise alignment. Regularly monitor and adjust alignment parameters to counteract the cumulative effects of operational stresses and vibrations. Engage in proactive maintenance by implementing continuous monitoring systems that can promptly detect and alert operators to any deviations from optimal alignment.
Cleanliness: Beyond routine cleaning, implement air purification and filtration systems in the operational environment. Proactively address potential sources of debris generation by enclosing sensitive areas or incorporating protective shields. Consider the strategic placement of cleaning systems, such as air jets or brushes, to ensure a continuous, proactive approach to maintaining a debris-free environment. By actively preventing the ingress of contaminants, you elevate the overall cleanliness standard, thereby extending the life of the industrial transmission belt.
Correct Storage: Optimize storage conditions by implementing climate-controlled environments for spare transmission belts. Incorporate smart storage solutions that mitigate the risk of physical damage. Utilize storage racks or cabinets equipped with humidity and temperature control systems. Implement an inventory management system that includes regular checks on the stored belts, ensuring they remain within optimal storage conditions and are ready for immediate use when required.
Temperature Control: Beyond basic temperature management, leverage real-time monitoring systems to capture nuanced temperature variations. Employ predictive analytics to anticipate potential temperature spikes or fluctuations. Integrate cooling solutions, such as fans or heat-dissipating materials, within the machinery to actively mitigate temperature-related stress on the transmission belt. By proactively managing temperature dynamics, you not only preserve the material integrity but also enhance the overall operational reliability of the system.
Avoid Overloading: Implement an advanced load monitoring system that provides real-time data on power demands. Integrate load sensors directly onto the transmission components to dynamically adjust for varying loads. Employ machine learning algorithms to predict load patterns and proactively adjust operational parameters to prevent overloading. By investing in intelligent load management, you not only protect the transmission belt from excessive stress but also optimize the entire system for sustained performance.
V-ribbed Belt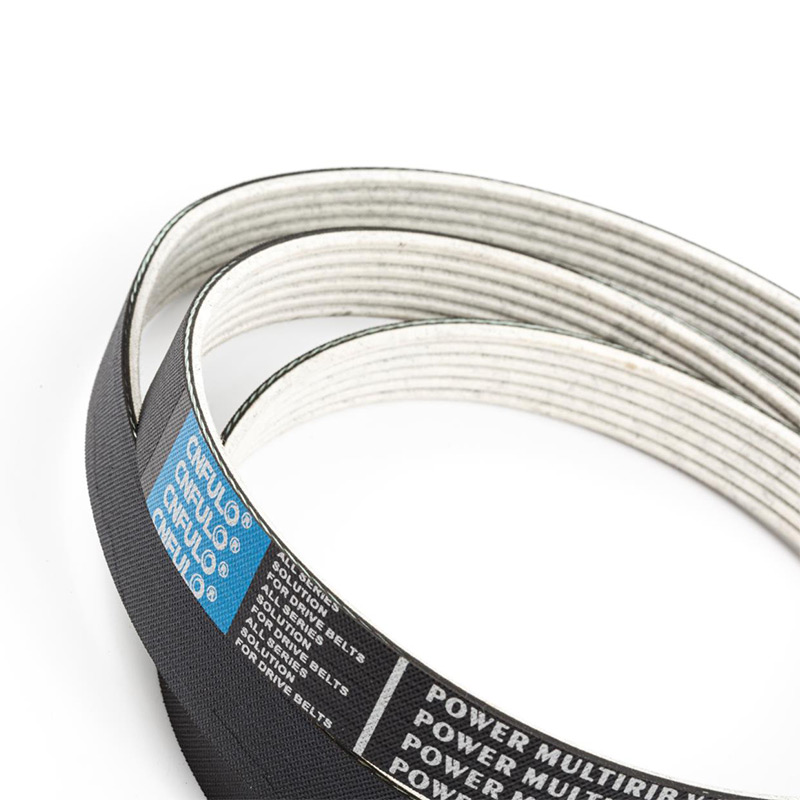