Summary:Addressing issues related to noise and vibration in carbon steel timing pulley applications involves a combination of design considerations, material selection, and proper maintenance practices. Here are several methods used to address these concerns......
Addressing issues related to noise and vibration in carbon steel timing pulley applications involves a combination of design considerations, material selection, and proper maintenance practices. Here are several methods used to address these concerns:
1.Balancing: Precision balancing is achieved through advanced manufacturing techniques and equipment such as dynamic balancing machines. Balancing ensures uniform mass distribution, preventing uneven forces that lead to vibration. Manufacturers employ stringent quality control measures to guarantee pulleys meet specified balance tolerances.
2.Damping Techniques: Engineers often utilize finite element analysis (FEA) to identify critical points in the pulley where vibrations are most significant. Strategic placement of rubber or elastomeric dampers at these points effectively absorbs vibrations, reducing noise. These dampers are carefully selected based on their material properties and designed to withstand the pulley's operating conditions.
3.Tooth Profile and Tooth Pitch: Employing advanced machining technologies like CNC (Computer Numerical Control) ensures precise tooth profiles and pitches. Any irregularities, such as uneven tooth spacing, are eliminated, minimizing noise during engagement with mating components like belts and gears.
4.Surface Finish: Achieving the desired surface finish involves employing grinding, honing, or polishing techniques. These processes yield smooth tooth surfaces, reducing friction and noise during operation. Quality control checks, such as surface roughness measurements, are conducted to ensure compliance with specified standards.
5.Alignment: Manufacturers employ laser alignment systems and precision measurement tools to verify proper alignment of pulleys within the system. Misalignment is corrected promptly during installation or maintenance to prevent excessive vibrations and noise. Detailed alignment procedures are often outlined in technical manuals provided by manufacturers.
6.Lubrication: Proper lubrication is crucial for minimizing friction and noise. Lubricants with high viscosity indices and exceptional film strength properties are chosen based on the specific application requirements. Lubrication intervals and quantities are meticulously calculated to ensure optimal performance and noise reduction over the pulley's lifespan.
7.Tensioning: Tensioning systems incorporate tension gauges and tensioning tools calibrated to industry standards. Manufacturers provide detailed guidelines for proper tensioning of belts, ensuring they operate within the recommended tension range. This prevents over-tensioning, which can lead to excess noise and premature wear, or under-tensioning, which can cause slippage and vibrations.
8.Material Damping Properties: Material scientists and engineers select carbon steel alloys with inherent damping properties, characterized by low elastic moduli and high internal friction coefficients. These properties dissipate vibrational energy, reducing noise levels. Advanced testing methods, such as dynamic mechanical analysis (DMA), help identify materials with optimal damping characteristics for specific applications.
9.Isolation: Vibration isolators, made from materials like rubber or neoprene, are strategically placed between the pulley system and surrounding structures. These isolators absorb and dissipate vibrations, preventing them from propagating to other components or the surrounding environment. Engineers conduct vibration analysis studies to determine the most effective isolator design for a given application.
10.Regular Maintenance: Establishing a proactive maintenance schedule is vital. Routine inspections, including visual checks, vibration analysis, and lubrication assessments, are conducted at specified intervals. Maintenance technicians follow standardized procedures outlined in maintenance manuals, addressing any anomalies promptly to prevent noise-related issues.
11.Simulation and Analysis: Utilizing advanced simulation software, engineers conduct virtual experiments to analyze the pulley system's behavior under various loads and operating conditions. Finite element analysis (FEA) and computational fluid dynamics (CFD) simulations help identify potential noise sources, allowing for targeted design modifications to minimize vibrations and noise levels effectively. Manufacturers invest in cutting-edge simulation tools and employ experienced simulation engineers to optimize pulley designs for noise reduction.
Timing Pulley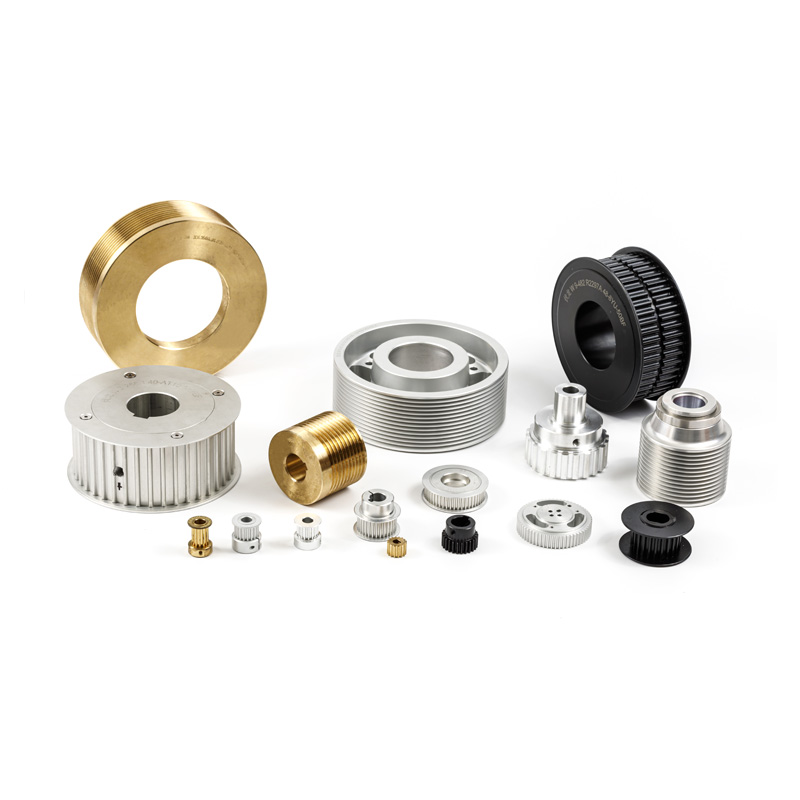