Summary:Industrial Cutting V Belts contribute to the efficiency of machinery in industrial settings through several key mechanisms:
Power Transmission Efficiency: Industrial Cutting V Belts are meticulously crafted to optimize power transmission efficiency w......
Industrial Cutting V Belts contribute to the efficiency of machinery in industrial settings through several key mechanisms:
Power Transmission Efficiency: Industrial Cutting V Belts are meticulously crafted to optimize power transmission efficiency within industrial machinery. The engineering involves precise calculations of belt dimensions, materials selection, and dynamic analysis to ensure minimal energy losses during the transfer process. The focus extends to reducing friction, considering belt flexure, and incorporating advanced technologies such as tooth profiles or special coatings to enhance grip and further boost overall power transmission efficiency.
Minimized Slippage: The V-shaped design of Industrial Cutting V Belts is a result of careful consideration to minimize slippage, a common issue in power transmission systems. The engineering involves in-depth analysis of contact mechanics, surface treatments, and material properties to achieve an optimal coefficient of friction. Additionally, advancements in manufacturing processes, such as precision molding and laser cutting, play a crucial role in creating belts with consistently effective grip, thereby minimizing any potential slippage during operation.
Flexibility and Adaptability: The exceptional flexibility of Industrial Cutting V Belts is achieved through a combination of material science and design innovation. Polymer blends with high flexibility are carefully chosen, and the belt structure is designed to accommodate bending around pulleys of varying sizes. Finite element analysis and stress simulations are employed to ensure that the belts maintain their structural integrity even under extreme flexing conditions, providing adaptability to diverse industrial setups with different spatial constraints.
Noise Reduction Technology: Industrial Cutting V Belts employ cutting-edge noise reduction technologies to address the challenges posed by operational noise in industrial settings. The engineering behind noise reduction includes the use of advanced damping materials, innovative tooth profiles, and precision manufacturing techniques. Computational models are often employed to optimize the belt geometry for noise reduction while maintaining mechanical integrity. The result is a system that not only efficiently transmits power but also operates with minimal acoustic impact, contributing to a quieter and more efficient work environment.
Low Maintenance Durability: The durability of Industrial Cutting V Belts is a product of materials science, metallurgy, and innovative manufacturing processes. Materials undergo rigorous testing for wear resistance, fatigue strength, and resilience to environmental factors. The belts are engineered to operate in conditions with minimal lubrication, and the incorporation of self-lubricating materials or coatings further reduces the need for maintenance. Predictive maintenance technologies, such as condition monitoring sensors, are often integrated to enable proactive servicing, maximizing the operational life of the belts.
Even Power Distribution: Achieving even power distribution in multi-belt drive systems involves intricate engineering and precise tensioning mechanisms. Computational models simulate the dynamic behavior of the belts under various loads, enabling engineers to design pulley systems that distribute power uniformly. Tensioning devices, such as automatic tensioners or dynamically adjustable pulleys, contribute to maintaining consistent tension across belts. The result is a synchronized system where each belt bears its proportional load, ensuring even power distribution and minimizing the risk of premature wear.
Temperature Resistance and Stability: Industrial Cutting V Belts designed for high-temperature applications undergo extensive testing in controlled environments and real-world conditions. Engineers select materials with high thermal stability, incorporating heat-resistant additives or reinforcements. Finite element analysis is employed to predict thermal expansion and contraction, ensuring dimensional stability under temperature variations. Thermo-mechanical testing validates the belts' performance in extreme temperature environments, providing the stability needed for reliable operation and contributing to the overall efficiency of industrial processes.
Bended V Belt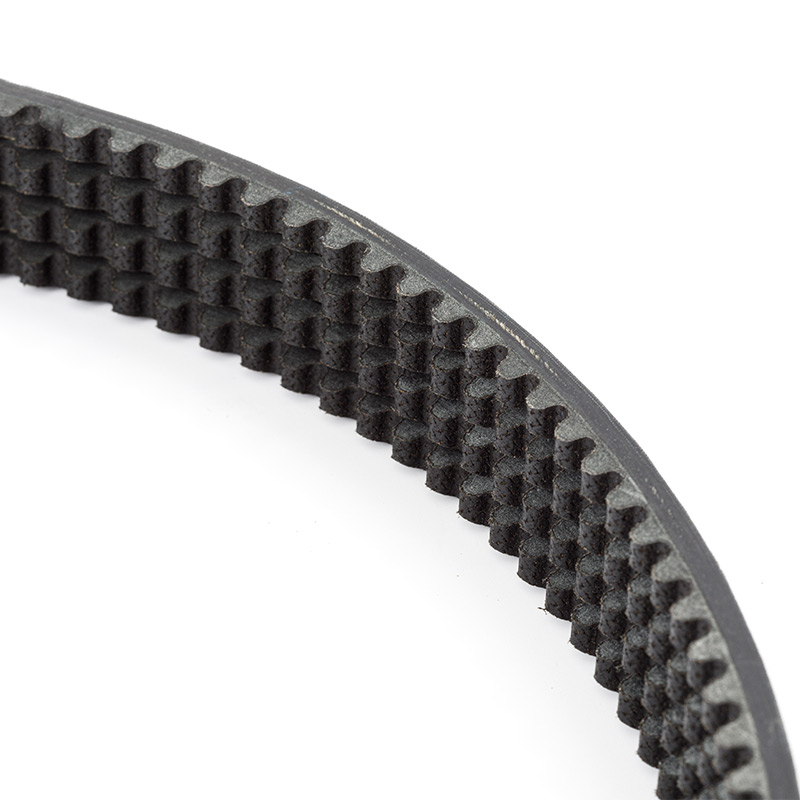